Efficient implementation of new processes: Overcoming overthinking
2 May 2024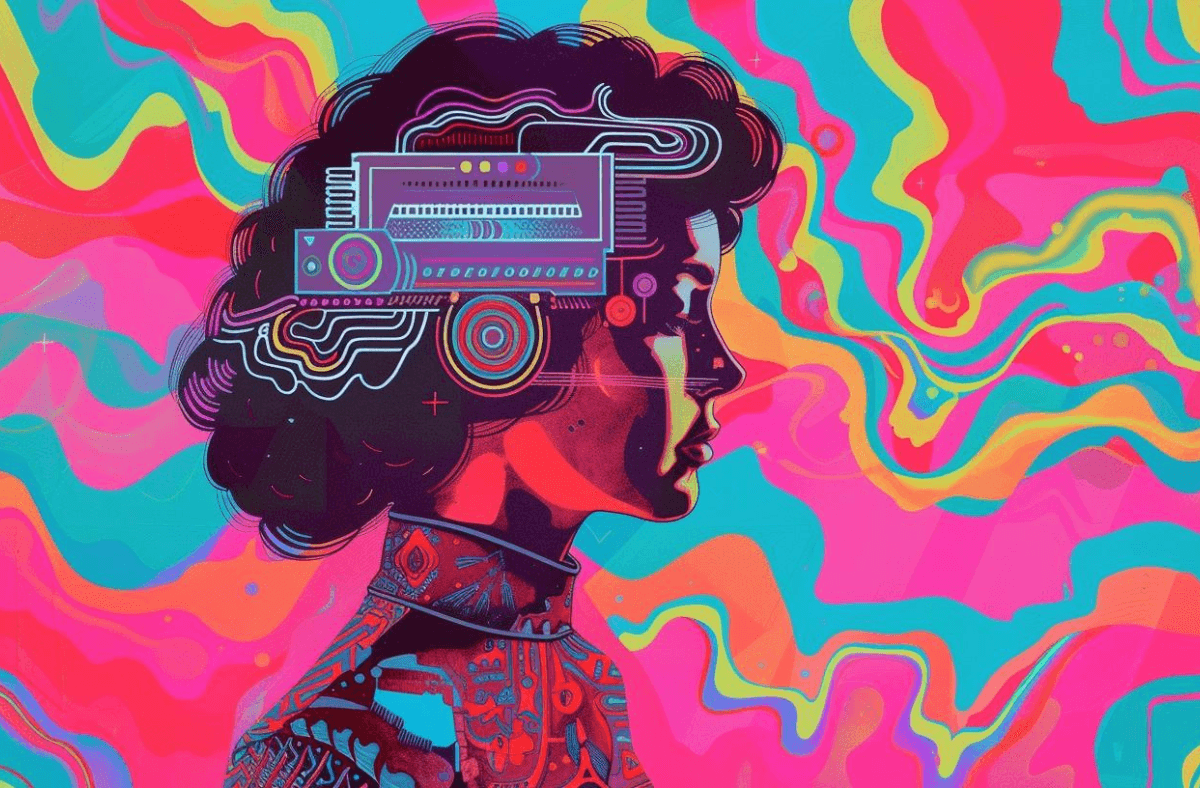
Why is it so difficult to implement a new tool or a process? (image by Midjourney)
Which new technologies show the most promise for process optimization, and what tends to be the biggest obstacle? We talk to Karol Łachacz, a manager with 10 years of experience responsible for operations and technology in the wood-based materials industry.
Autentika: Could you share specific examples from your career where implementing new tools or automation significantly improved efficiency and work quality?
Karol Łachacz: Automation doesn't always have to involve computers, IT systems, robotics, or complex machinery. It's more about streamlining work, making it automatic wherever possible, without absorbing more attention than necessary – without falling into routine.
From my experience, I've found that cumulative small changes have a greater impact in the long run than individual, large innovations. In industrial and manufacturing environments, introducing many small automations and fostering a mindset that provokes automation bring greater value.
Simple solutions and automations we implemented with the team at the chipboard factory included technological, technical, and operator checklists, as well as verification and control lists. Such implementations are always based on understanding the essence of routine tasks and adapting to changing conditions. Regardless of the form, it's crucial to understand why we take specific actions and why it's worth carefully performing seemingly simple tasks. That's when the biggest changes happen – we begin to understand the meaning and purpose of our actions and consciously carry them out despite the routine.
It's worth mentioning that the evolution of these solutions continues to this day. Some actions, like the aforementioned checklists, started on paper but were eventually transferred to IT systems supporting automatic control and supervision – reminding us of tasks and generating lists. Others remain on paper today and effectively fulfil their function in that format.
There are areas where the psychological aspect of responsibility for a task is significant – someone takes a pen and confirms responsible task completion with their name.
How were the above processes measured?
In the chipboard factory, hard data is crucial – the plant is meticulously metered, and the used indicators constantly evolve. Take, for example, the target of maintaining machine operation at 95.0% – this includes the time allowed for planned maintenance, order changes and necessary servicing. If the level falls below the set target, we analyze what influenced this. Perhaps there were things that we could have avoided through more frequent routine inspections? Measures such as deliberately conducted technical tours and operator checklists help to improve technical availability, and better utilization of the machinery leads to an improvement in production costs in the long term.
Read also: What’s the gold standard for a discovery process? See our exemplary approach – BBUD
What new technologies or tools do you consider most promising for process optimization and automation in the coming years?
In the furniture and wood industry, my current field of work, artificial intelligence certainly plays an important role and will continue to do so. I increasingly see self-learning algorithms in production-related areas that are able to draw conclusions from the data collected. Machinery is increasingly "wired" and measured, and the data collected in real-time exceeds human capabilities. Artificial intelligence can efficiently perform analytical tasks, identify trends and warn of alarming symptoms.
However, I believe that effective use of this data still requires collaboration with humans, especially in the development of proposals and policies. We have specialists today who can organoleptically assess how long the bearing housing will continue to function by touching it. However, technology allows us to streamline this process.
Analysing the condition of machines is faster and more efficient today than it was a few years ago. Although the role of the expert is still indispensable, artificial intelligence makes it possible to shift human work to other tasks while monitoring and detecting anomalies and suggesting possible solutions.
Read also: Business apps: A geek's checklist
What are the biggest challenges you see in your work? What is the most common obstacle, the roadblock that impedes positive changes and transformation? Do you notice any mistakes that organizations make in their approach to automation and process optimization?
I believe that a major obstacle in many areas is still the inertia of bureaucracy and decision-making processes. Waiting for regulatory approvals can take months or years, and in a dynamic business environment this can be problematic, especially for innovative technologies.
Another limitation I observe in my daily work is what I call "overthinking" – over-analysing every possible aspect and outcome of actions, every worst-case scenario. In the long run, this hinders progress and decision-making, because everything requires consultation, validation, everyone has to agree, express an opinion, everyone has to contribute, comment and give detailed answers to all doubts, and the process does not move forward. This is where common sense comes to the rescue, understood as a balanced analysis of opportunities and risks.
We are talking more about the management level here, but you have also been involved in building teams in your career. How do you build a team that is not afraid of experimentation and change?
By supporting them in preparing for and during experiments and changes. For this to happen, however, creating a safe working environment should be a priority. In a dynamic business environment, a sense of safety, understood as organizational support and support from superiors, is crucial for making bold decisions, experimenting and seeking unconventional solutions. When we discuss the need for change and decide to experiment, we create a shared contract to share responsibility for the outcomes, including the unforeseen and potentially unfavorable ones.
In the broader context of building a change-oriented culture, openness starts with the mindset of leaders and managers, who should demonstrate that they are not afraid of new things. A leader who openly acknowledges that they are not afraid of change, but also recognizes that they do not have a monopoly on knowledge, listens and constantly seeks inspiration, can attract, retain and develop outstanding minds over the long term.
Why is it so difficult to move from theory to practice – knowing how to introduce a change or new process and then actually implementing it?
I don't quite agree with the idea that the transition from theory to practice is the problem. In my opinion, the problem lies one level higher, namely at the level of ideas, concepts and assumptions regarding the implementation of a solution.
The implementation process is often treated as a linear process, from point A (theory and assumptions) to point B (practice and implementation), although parallel processes can be more effective. To implement something effectively, one must not be afraid to experiment, and openness to change, as we have already discussed, is an essential part of this process.
Of course, every case will be different, but a common denominator in many projects is that assumptions change quickly (much like the reality around us). Therefore, flexibility and a willingness to adjust course are essential. I believe that doing theory and practice at the same time has the potential to yield better results in the long run, especially if we apply the small steps method. This way, even if we make a few small mistakes, we can pull back in time and correct course.
Read also: How AI benefits Warehouse Management Systems (WMS)
Let us talk a little about the tools themselves. Which approach do you prefer – ready-made digital tools or those that have been developed for specific needs?
That depends. With the standard functions of many tools, ready-made solutions are often sufficient. In my opinion, however, this mainly applies to areas that can be standardized regardless of the industry. For example, task management tools where the functions are similar and the choice depends on the user's individual preferences, expectations in terms of intuitiveness, visual design, etc.
But wherever the tool needs to support a particular goal, specific to a particular industry, area, territory, location in the factory or a particular machine – this is where my experience shows that customized solutions that are "tailor-made" are incomparably more effective. In the highly automated production area where I work, manufacturers of production equipment and technology suppliers present new digital improvement proposals every few months. Most of them are designed to cover the widest possible group of potential users in a universal way. Therefore, it is more advantageous to develop customized tools using your own resources as much as possible, which also promotes the development of organizations and teams. However, as I have already mentioned, it is important to ensure adequate support for such measures and to share responsibility for the impact.
If you could implement a digital tool overnight to solve an urgent problem, which one would you choose?
If we could fantasize in this regard, I would like to choose a tool that serves as a common sense filter for all matters. That's my favorite unit of measurement and review – an immeasurable, subjective filter that leads me to make the right decisions, which I often look back on with satisfaction. Despite my interest in technology and artificial intelligence, I believe that common sense will always set us – humans – apart. Perhaps such a "digital verifier of common sense" would be useful for all of us.
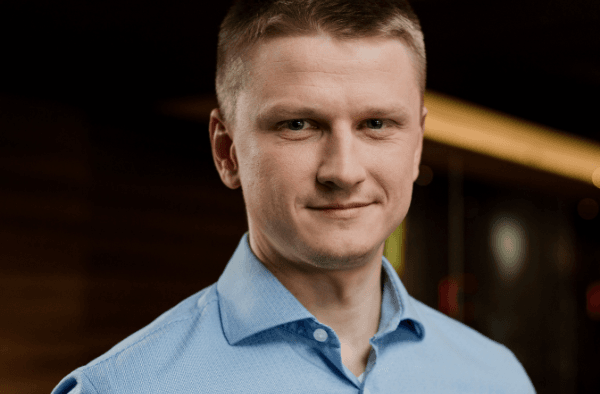
Karol Łachacz – a carpenter by trade, an engineer by education, and a manager with 10 years of experience in the furniture industry, specializing in production, technical, and manufacturing technology. Currently a board member at Tanne sp. z o.o. (part of the Fabryki Mebli Forte S.A. Capital Group), responsible for operations and technology in the wood-based materials industry. He approaches digitization, automation, and modern technologies with an open mind, focusing on implementing those that bring added value to users and the company. A passionate advocate for interpersonal relationships and social psychology, he places human potential on par with technological advancement. He considers the most effective changes in the industrial production environment to be those that, with the use of modern tools, support the comfort and efficiency of human work.